Вы оптимизируете свой парк техники? Или идете на компромиссы?
Многие компании используют смазочные материалы известных брендов, которые не всегда создаются с учетом особенностей конкретной области применения

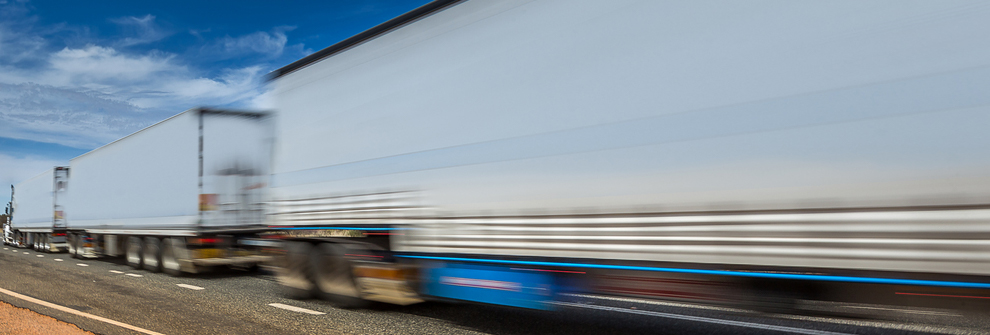
Недавно один наш бывший клиент из Канады потерял независимость и продал компанию конкуренту. Столкнувшись с дефицитом бюджета, он начал принимать решения, исходя исключительно из цены, стал использовать более дешевые масла и применять единый регламент технического обслуживания ко всему парку техники. Вместо экономии такой подход привел к противоположному эффекту — незапланированным простоям оборудования и повышению расходов на техническое обслуживание. В результате это переросло в перебои в работе и потерю клиентов. Бизнес стал нерентабельным, и у клиента не осталось другого выбора, кроме как продать его. Новые владельцы отобрали лучшие активы парка техники и оставили некоторых сотрудников. Остальные ресурсы были ликвидированы.
Эта история может послужить уроком для операторов парков техники по обе стороны границы. Многие управляющие покупают смазочные материалы известных брендов, которые не всегда соответствуют особенностям области применения, условиям эксплуатации или целям технического обслуживания конкретного парка техники. Такой подход не позволяет управляющим оптимизировать интервалы замены, топливную экономичность и время простоев. В результате они теряют деньги.
Давайте рассмотрим пример с другой компанией, которая провела оценку своих методов смазки. Автопарк компании включал 1000 грузовиков класса 8, замена моторного масла выполнялась с интервалом в 35000 миль пробега. В среднем в год на каждое транспортное средство в парке приходилось 2–3 замены моторного масла и комплекта фильтров. Расход моторного масла на каждый грузовик составил 11 галлонов, стоимость галлона масла в среднем составляла 7,5 долларов США. День простоя из-за технического обслуживания стоил им 2000 долларов США на грузовик.
Что все это значит в долларах? Используя низкокачественные смазочные материалы и не оптимизируя интервалы замены, они выполняли одну замену масла и фильтров в год, которая стоила им около 90000 долларов США. Кроме того, день простоя каждого грузовика в парке выливается в 2 млн долларов США в год. А поскольку используемое ими масло не способствовало сокращению расхода топлива, они тратили на топливо лишние 643 доллара США в год на грузовик или 643000 долларов США на весь парк. Это составляет 1,7 % от годовых расходов компании на топливо.
Но не все так печально. Проведенная оценка выявила потенциал для сокращения расходов примерно на 2,7 млн долларов США в год за счет оптимизации интервалов замены, топливной экономичности и времени простоев.
Безусловно, непросто следовать таким современным тенденциям, как переход на маловязкие масла, регламентам EPA в отношении парниковых газов (GHG), новым OEM-спецификациям и оптимизировать интервалы замены. Однако оценка методов смазки, применение оптимальных смазочных материалов, созданных для конкретной области применения, и увеличение интервалов замен позволили многим руководителям парков техники сэкономить миллионы долларов. Кроме того, это оказало положительное влияние на такие бизнес-показатели, как время безотказной работы, средняя стоимость мили пробега каждого грузовика, стоимость перевозки тонны груза и срок службы оборудования.
Экспертные консультации по новым технологиям в сочетании с протоколами испытаний помогут вам подобрать подходящую продукцию и оптимизировать интервалы замены, топливную экономичность и время простоев. Вы будете спокойны и уверены в том, что эксплуатируете технику в соответствии с рекомендациями OEM и способствуете повышению ее производительности.